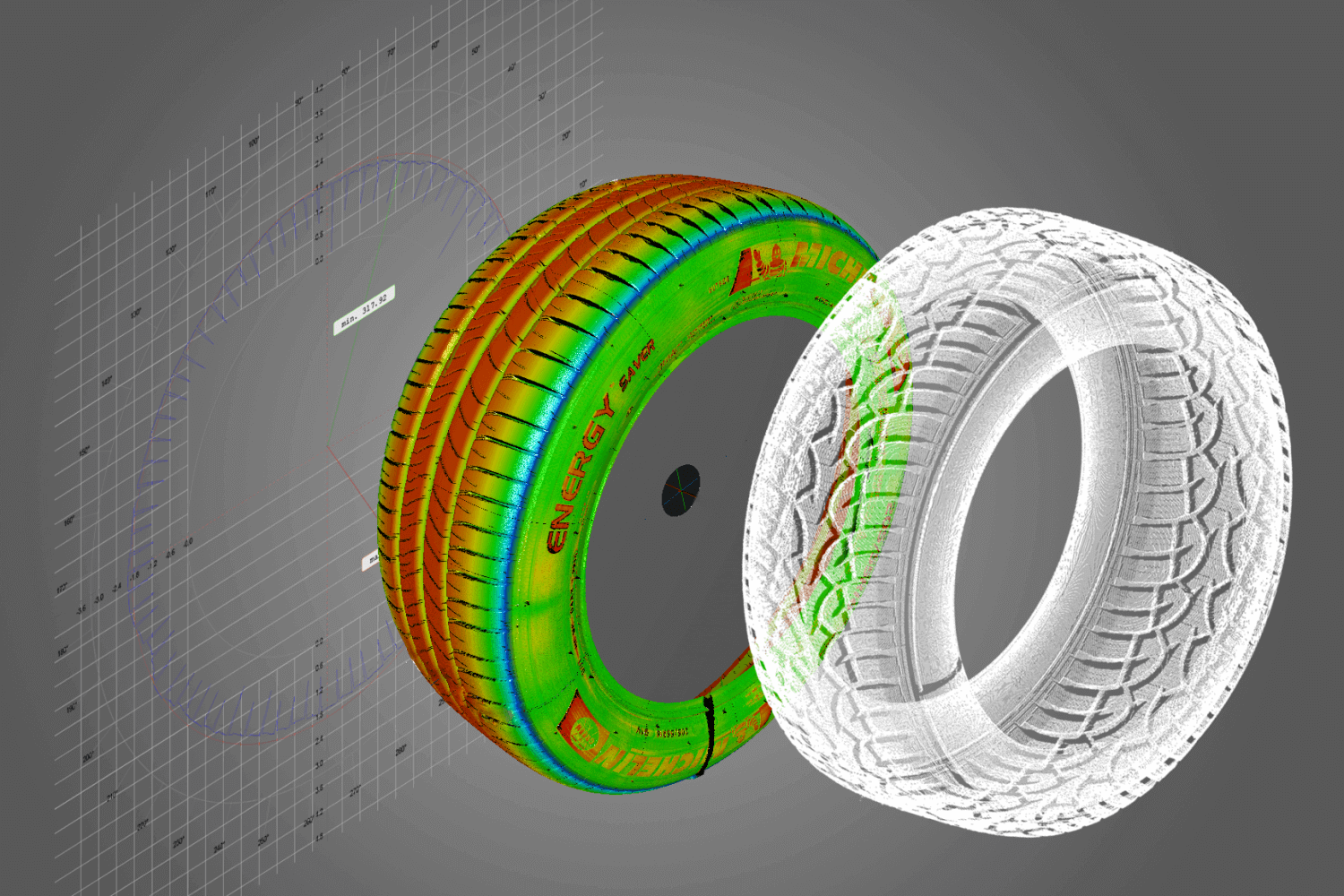
The 3D mapping function enables wear analyses and predicts the service life of a tire by continuously measuring and comparing the decreasing tread depth. With just a few measurements at different mileages, the total tire mileage can already be extrapolated. Automobile manufacturers, tire developers and test centers use the TriScan Tire for their product classification and development, as well as for quality assurance and final sampling inspection.
The concept includes a point laser triangulation sensor, a driven wheel holder for centric mounting of the measuring objects (tyres & rims) and a three-axis sensor positioning unit. Countless analysis, calculation and visualization functions for the profile evaluation of new and used tires make the TST what it is, an established, user-friendly and representative measuring method, as it is appreciated by its users.
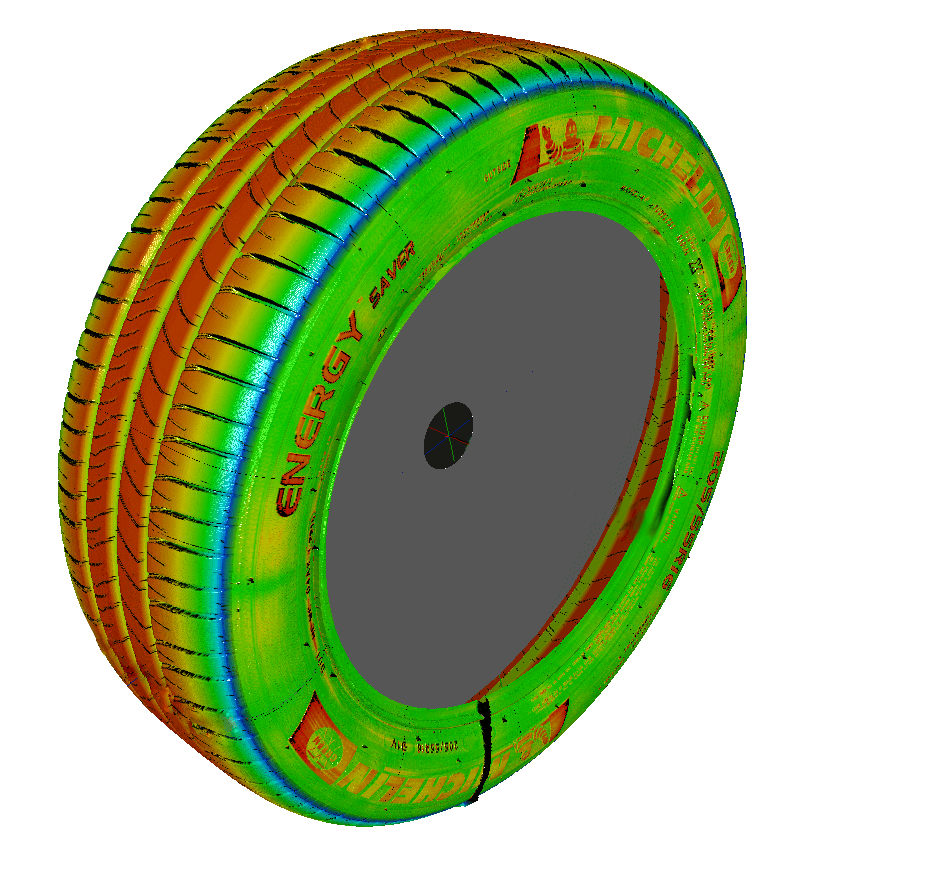
Software:
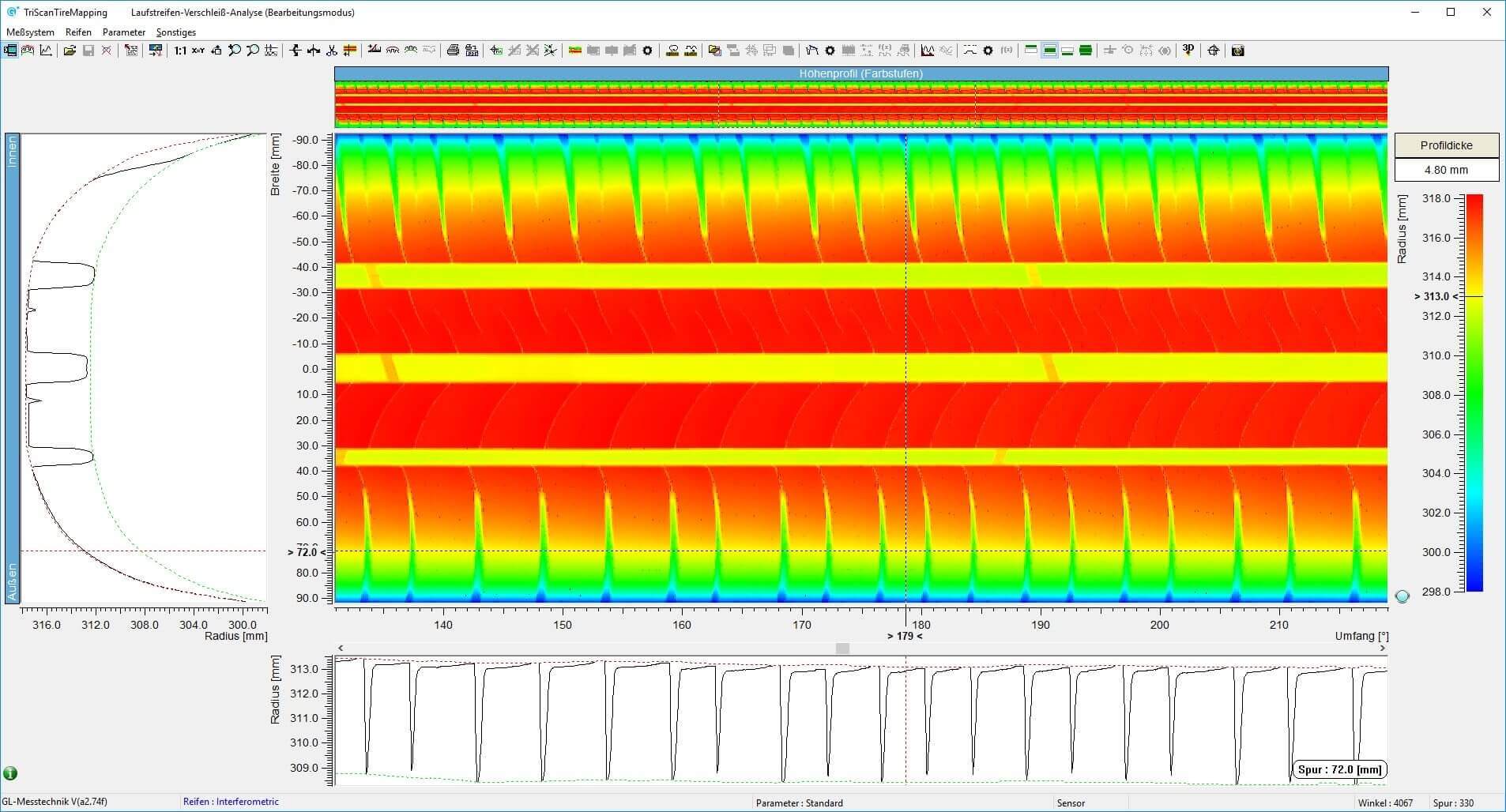
Specification
- Measurement technology: Triangulation-Point-Laser-Sensor
- Laser: Visible / Red
- Laser Class: IIM /IIIB
- Data transmission: Digital
- Tire types: PCR / LTR / TBR / OTR / MC / Carting
- Rim size: 13‘‘ -23‘‘(other sizes optional)
- Tire width: upto 550 mm (other sizes optional)
- Tire diameter: upto 1300 mm (other sizes optional)
- Tire weight: 70kg / 400kg / 1000kg
Hardware features
- Digital Laser Sensor
- Non-contact measuring method
- Point controlled laser intensity
- Cyclical and linear movement of the axes
- Collision protection system between product and sensors
- High-precision linear guides with recirculating ball screws
- Manual tire positioning
- Automated measuring process
- Rotatable measuring head
- Laser cross projection for optimized product alignment
- Universal rim clamping sets for centric product assembly
- Rim pressure flange for homogeneous contact pressure
- Industrial and WINDOWS based computer system
- Floor installation with heavy-duty anchors
- Selected and durable standard components
- Production and quality “Made in Germany
- Tire recording camera system
- Optional accessories
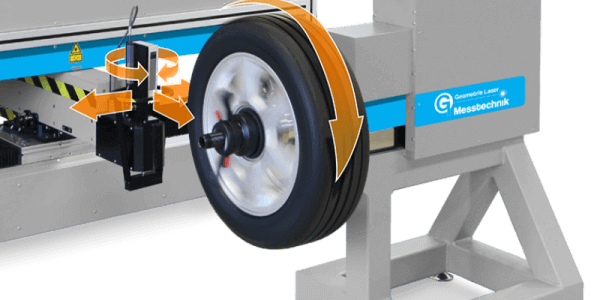
